Bolts are essential components in countless applications, from construction to automotive engineering. Understanding how different types of bolts are manufactured not only sheds light on their quality and performance but also helps in selecting the right fastener for specific needs. This article explores the various manufacturing processes behind bolts, highlighting the significance of material choice, design, and production techniques in creating reliable and durable fasteners.
Overview of Bolt Manufacturing
Bolt manufacturing involves several critical processes to produce reliable fasteners. Each type of bolt has a specific method tailored to its design and application needs.
- Material Selection
Material choice influences a bolt’s strength, corrosion resistance, and durability. Common materials include carbon steel, stainless steel, and alloy steel. Each material has unique properties that suit different environments. - Forging Process
Forging shapes the bolt from heated metal. This process increases density and strength. Open-die and closed-die forging are standard methods. Open-die forging involves molding metal between two large dies, while closed-die forging uses a cavity to create precise shapes. - Machining
After forging, machining refines the bolt’s dimensions. Processes like turning, milling, and drilling ensure that bolts meet specific tolerances. These steps create threads and other necessary features for bolted connections. - Heat Treatment
Heat treatment enhances the mechanical properties of bolts. Processes like quenching and tempering alter the bolt’s hardness and ductility. This treatment ensures that bolts withstand loads and reduce the risk of failure. - Surface Treatment
Surface treatment protects bolts from corrosion. Techniques include galvanizing, plating, and coating. These treatments provide a barrier against environmental elements, extending the bolt’s lifespan. - Quality Control
Quality control measures guarantee that bolts meet industry standards. Inspections at various stages identify potential defects. Common tests include tensile strength, hardness measurement, and dimensional verification.
These processes collectively ensure the production of high-quality bolts suitable for a range of applications in construction and automotive engineering.
Types of Bolts
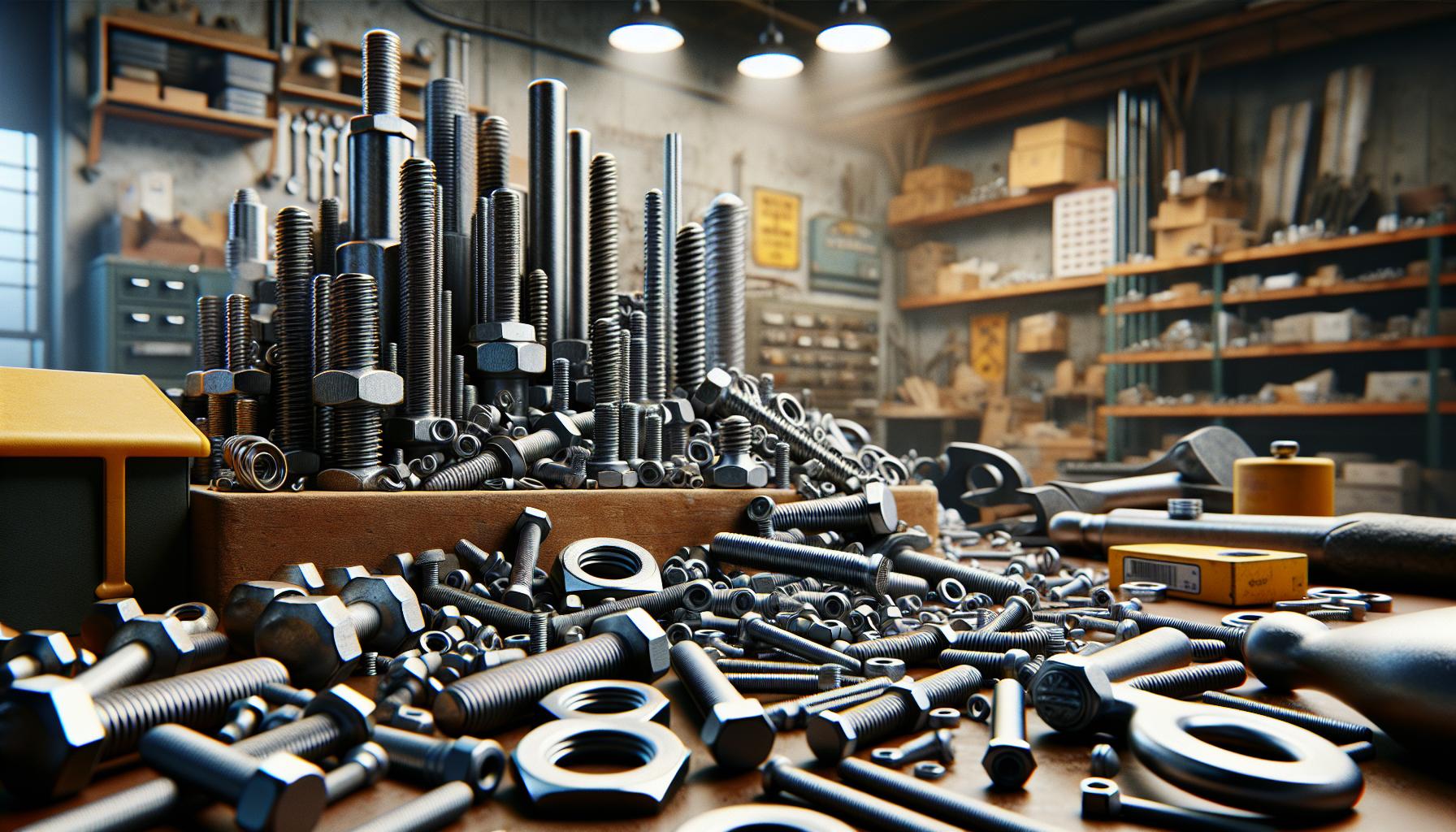
Bolts serve different purposes in construction and manufacturing, categorized mainly into standard bolts and specialty bolts.
Standard Bolts
Standard bolts follow established specifications, including dimensions, thread forms, and material types. Common types include hex bolts, carriage bolts, and lag bolts. These bolts are widely used for general fastening applications. Their predictable dimensions and tensile strengths make them suitable for construction projects, machinery assembly, and automotive applications. The manufacturing process for standard bolts includes forging or machining, heat treatment, and surface finishing to improve durability and corrosion resistance.
Specialty Bolts
Specialty bolts cater to specific applications requiring unique designs or materials. Examples include shoulder bolts, U-bolts, and eye bolts. These fasteners often undergo additional processes, such as custom machining or specialized coatings for enhanced performance. Manufacturers tailor the design, size, and materials to meet particular needs, ensuring optimal functionality in demanding environments. Specialty bolts may also be produced in smaller quantities, necessitating precise manufacturing techniques to meet specific customer requirements.
Manufacturing Processes
Manufacturing processes for different types of bolts encompass several specialized techniques tailored to improve functionality and durability.
Cold Heading
Cold heading involves shaping metal at room temperature, allowing for efficient production without altering the material’s properties. This process uses dies to mold wire or rod stock into bolt shapes through high-speed impacts. Cold heading is particularly suitable for manufacturing bolts with consistent dimensions. This technique often results in high-strength products with minimal waste. The affordable nature of cold heading makes it popular for producing standard bolts like hex and socket-head types.
Hot Forging
Hot forging entails heating metal above its recrystallization temperature, improving malleability and enabling complex shapes. This method allows manufacturers to create larger bolts with superior mechanical properties. During hot forging, metal is shaped and then rapidly cooled, enhancing its strength and reducing brittleness. This process supports the production of structural bolts that endure high-stress applications. The ability to use alloy steels in hot forging also allows for customized properties, catering to specific construction or automotive requirements.
Machining
Machining is a precise manufacturing process that involves removing material from a workpiece to achieve exact dimensions and surface finishes. Common machining techniques include turning, milling, and drilling that refine bolts into their intended shapes. This process is essential for specialty bolts that require tight tolerances or unique features. Machining permits the creation of custom threads, grooves, or heads that standard processes cannot provide. Additionally, after initial shaping, machining can improve surface quality and improve corrosion resistance, ensuring performance in demanding environments.
Quality Control in Bolt Manufacturing
Quality control in bolt manufacturing ensures bolts meet stringent industry standards for safety and performance. Employing a range of measures, manufacturers conduct inspections and tests throughout the production process.
Inspection of Raw Materials
Inspection starts with raw materials. Suppliers provide documentation certifying material quality. Manufacturers perform tests for tensile strength, hardness, and chemical composition to verify compliance with specifications.
Dimensional Accuracy Checks
Dimensional accuracy checks occur at multiple stages. Manufacturers use calibrated measuring tools, such as micrometers and calipers, to confirm proper dimensions. A deviation of even 0.01 inches can lead to performance issues in bolts.
Visual Inspections
Visual inspections detect surface defects. Operators look for issues like cracks, pits, or rust that may compromise structural integrity. Defective bolts are removed from the assembly line, ensuring only quality products proceed to the next stage.
Mechanical Testing
Mechanical testing evaluates performance properties. Common tests include tensile tests, which measure how much a bolt can withstand before breaking, and shear tests that assess resistance to sliding forces. For example, a typical Grade 5 bolt must meet a minimum tensile strength of 120,000 psi.
Surface Treatment Quality Checks
Surface treatments also undergo quality checks. Treatments like zinc plating or powder coating protect against corrosion. Manufacturers test the adhesion and thickness of these coatings to ensure durability in various environments.
Final Inspection and Certification
Final inspections verify compliance with specifications and customer requirements. Manufacturers use inspection reports and certificates of compliance as part of their quality assurance process. These documents demonstrate adherence to industry standards, such as ISO 9001.
Continuous Improvement
Continuous improvement processes refine quality control. Manufacturers regularly review inspection data to identify trends and areas for enhancement. Training employees on proper quality control practices fosters a culture of accountability and precision.
By implementing rigorous quality control measures, manufacturers produce high-quality bolts that perform reliably in critical applications.
Conclusion
Understanding the manufacturing processes of different types of bolts is essential for ensuring their quality and performance in various applications. From the selection of materials to the specific techniques used in forging and machining, each step plays a critical role in producing reliable fasteners.
With advancements in technology and quality control measures, manufacturers can create both standard and specialty bolts that meet stringent industry standards. This commitment to excellence not only enhances the functionality of bolts but also ensures safety in critical applications. By appreciating these manufacturing intricacies, one can make informed choices when selecting bolts for any project.
Frequently Asked Questions
What is the importance of bolts in construction and automotive engineering?
Bolts are essential fasteners that secure components in construction and automotive applications. Their reliability impacts safety, structural integrity, and overall performance, making them critical in these industries.
What are the key factors in bolt manufacturing?
Key factors in bolt manufacturing include material choice, design specifications, and production techniques. These elements directly affect the quality, durability, and performance of the final product.
What materials are commonly used for bolts?
Common materials for bolts include carbon steel, stainless steel, and alloy steel. Each material offers unique properties, such as corrosion resistance or strength, suited for specific applications.
How do manufacturing processes affect bolts?
Manufacturing processes like forging, machining, and heat treatment significantly influence the strength and durability of bolts. Proper techniques ensure that bolts meet industry standards and function effectively.
What are standard and specialty bolts?
Standard bolts, like hex and carriage bolts, are used for general applications, while specialty bolts are designed for specific needs, featuring unique designs and materials to meet particular performance requirements.
What is cold heading in bolt manufacturing?
Cold heading is a process that shapes metal at room temperature, producing high-strength bolts with minimal waste. This technique is ideal for creating standard bolts efficiently.
What is hot forging and when is it used?
Hot forging involves heating metal to enhance malleability, allowing for the formation of larger bolts with superior mechanical properties. It’s commonly used for bolts that endure high-stress conditions.
Why is quality control important in bolt manufacturing?
Quality control ensures that bolts meet safety and performance standards. Rigorous inspections and testing at various stages of production confirm that bolts are reliable and defect-free.
How are bolts tested for quality?
Bolts undergo several tests including tensile strength evaluations, chemical composition analysis, dimensional accuracy checks, and surface treatment inspections to ensure they meet industry standards.
What role do surface treatments play in bolt performance?
Surface treatments protect bolts from corrosion and wear, enhancing their durability. These treatments can improve the bolt’s resistance to harsh environments and extend its lifespan.